The ergonomics of the kneeling chair design intend to assist in maintaining proper orientation of the pelvis to support the spine. Although common designs allow for this, it is common for the seat’s orientation to permit the body to slide forward so that the knees carry body weight. After a while, this becomes quite uncomfortable. The intent is structurally appropriate, but the implementation is often insufficient. (There are versions of this available with a horizontal seat, but then the knee rest needs to be adjustable to the leg length – a significantly more complex structure.)
Another example of an ergonomic seating device is the Yoga Ball. These easily allow for the hips to orient to effectively support the spine while offering the additional advantage of being somewhat unstable, requiring that you maintain an active posture. You cannot let your body go to sleep while sitting on a Yoga Ball.
At the base of our pelvis are a pair of bones called Sit(z) Bones. When we rest the weight of our torso on these bones the pelvis is positioned correctly to support our spine. Our ancestors, when not squatting, sat on rocks or logs and consequently, the tissue at the sit bones was tough enough to support their body weight. Without this tissue being conditioned, sitting thus can be somewhat uncomfortable. As a result, we adapted our surroundings to sit on broad soft cushions that distribute the weight of the torso across the buttocks. Doing so dulls the feedback informing the reflexes that support aligned posture and compresses the vascular and nerve (Sciatic) supply to the legs.
There is a post discussing the Sit Bones in more detail here: SITTING
It is much better to simply sit on a stool high enough so that the knees are lower than the pelvis. Even better is a stool hard enough so that you can feel your sit bones (Ischeum). This provides a solid foundation that the spine can optimally organize above. The flat surface of the stool seat provides a much more beneficial contact surface than the sloped seat of a kneeling chair, or even an expensive “ergonomic” office chair. It might take some “getting used to” but this posture is known to maximize our myriad regenerative potentials.
Kneeling on the floor has always felt comfortable for me. This is sometimes called a Japanese style of sitting. I have contemplated the design of a supportive stool to use when working on the floor at a low table for quite some time. This would simply be a board ~8″ above the floor to rest my sit bones on and tuck my legs under instead of a cushion – which has never worked well for me. Considering this as a woodworking project, I was stumped by the joint between the vertical and horizontal, which I could not envision as capable of managing the mechanical stresses involved. Recently it occurred to me that I could try 3D printing this joint and it might manage the loads involved. To my surprise, it worked quite well.
I don’t know if it is merely because I made this, but I find sitting on this stool to be very soothing and comfortable. It is somehow freeing to be on the floor in this posture, and this stool is my new favorite piece of furniture. Having your center of gravity up off of your heels is a more dynamic sitting posture. Unfortunately, now all of my other furniture is the wrong height. There may be a future version of this where I modify a standard office chair, something like this example, but aligned more closely with the issues discussed in this post: Kneeling Chair.
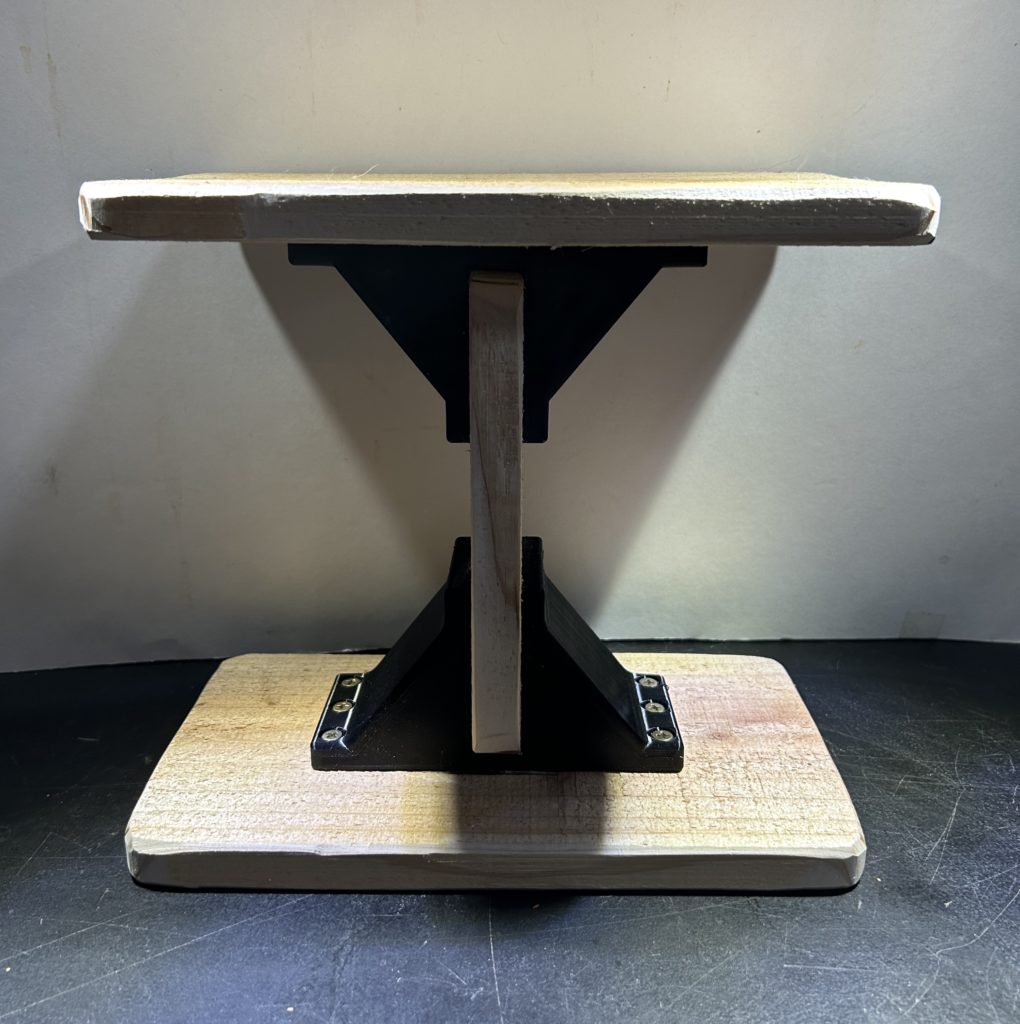
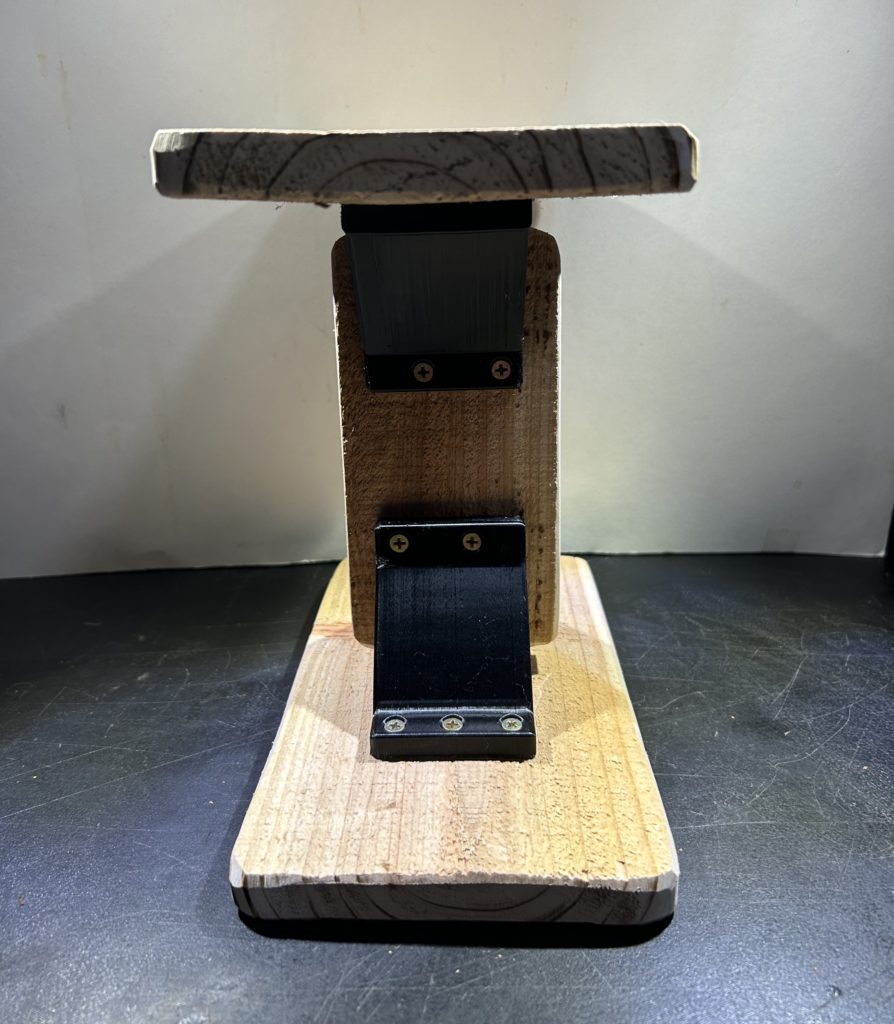
DIY Stool
Included here is an STL to print a pair of these joints. These are designed for standard 3/4″ lumber.
The principle print consideration is to print these on their side so that every layer has the whole profile of the joint (screw holes do not face the print surface).
This prevents a weak structure in the load dimension.
I added some silicon adhesive when assembling to inhibit creep in the articulations. Screws in the horizontal pieces are very short so that they don’t poke through (3/4″).
In the vertical joints, these are long enough to grab the joint on the opposite side (1 1/4″).
I estimate this design is rated to at least 250 lbs. centered over the vertical strut, but no formal testing has been done.
DO NOT STAND ON THIS – FOR SITTING ONLY
STL of the Joint for 3D Printing:
These can be ordered from any of the many 3-D PRINTING COMPANIES
StoolJoint.stl
Material: PLA or stronger
Infill Density: 20%
Qty: 2
by providing the STL’s in the links above.